What's Echizen Urushi
- Scratched urushi tree
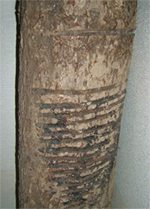
- Tools for collecting urushi
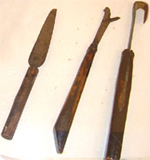
"Urushi" is the sap of the urushi tree ( its scientific name is Rhusverniflua). There are urushi tappers called "urushi kaki shokunin (shokunin means a person who specializes in something)" and they collect the sap by making scratches on the tree's surface with special knives. Urushi tree exudes its sap from the scratches to fix the damage. Using the mechanism of an urushi tree, the small amount of sap, approximately 200cc per tree, is collected trough a year. After the harvest, urushi kaki shokunins cut down the urushi trees and plant them again. Even thought the amount of the sap is small, the ability of urushi lacquer comes in handy.
Other than use as lacuqer, urushi is used as glue. Urushi has an interesting characteristic in its drying process. Substances in the thick liquid urushi react to oxygen in air and the chemical reaction hardens the liquid. It is different from the simple drying process that reduces moisture from a solid by heat and wind. Once it hardened, it's not easy to remove. Urushi is quality natural glue strong against acid, alkali, oil and water.
The powerful urushi sap was mostly harvested in Echizen area (today Sabae City in Fukui Prefecture), and Echizen Urushi is developed in the area. Echizen Urushi is traditional handmade wooden items made by coating its wooden base with urushi lacquer. Although it is recognized as tableware, it comes in many different forms such as bowls, plates, boxes, trays, vases, chopstickss, furniture and many different arts and crafts. The shokunin in Echizen have enhanced their skill to create Japanese lacquerware, and Echizen became one of the biggest lacquerware production area.
Lacquerware combines both beauty and functionality. It is displaying a beautiful glossy surface that is created by urushi topcoat. It is said that “urushi” is named after Japanese language,"uruwashii" or "uruoshi," that means something beautiful and glossy. Furthermore, wooden tableware is very light to hold, and has its special warmth and touch indescribable by words. Japanese have been very fond of these characteristics especially because they hold plates and bowls in their hands when they eat. Because wood has very low heat conductivity, lacquerware is excellent in insulation which enables to keep the food inside warm for a long time without bringing heat directly to hands holding it. It is the balance of function and design that makes Japanese lacquerware very special.
Recently, besides natural wood, new material has been developed by adding plastic to grinded wood which enabled mass production with low cost especially suitable for business use. Besides the natural opal color of urushi, lacquerware of different colors such as red, black, and amber and made by adding various dyes in urushi. Nowadays, sap of exuded from mango or cashew trees and artificial varnish similar to urushi lacquer are also sometimes used.
- The location of the main Echizen Urushi industrial area
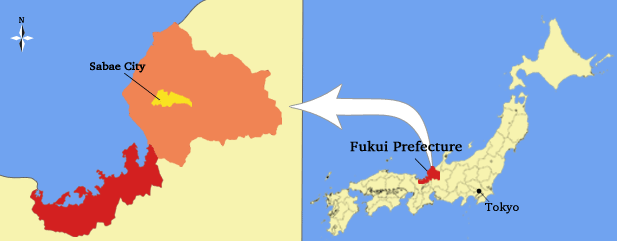
*The former Echizen area is in orange.
The Roots of Echizen Urushi
- The replica of the emperor's crown
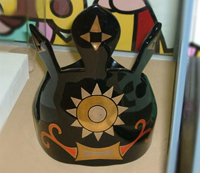
Lacquerware manufacturing in Echizen is one of the traditional industries in Japan, and its history dates back over 1,500 years. It is recognized that people in Fukui Prefecture used lacquerware since the Yayoi Period. The oldest Japanese lacquerware was discovered at Torihama Shell Heap in Fukui Prefecture. There are also some stories implying that Fukui Prefecture is the oldest lacquerware production area.
In 527A.D., when the 26th emperor of Japan was young, he ordered a lacquerware craftsman in Echizen to repair his crown. The craftsman had repaired the crown beautifully using the urushi lacquer, and had also presented him with a handmade black lacquered bowl as a special gift. The emperor was deeply impressed by its beauty and ordered the people in Echizen immediately to spread their technique widely across Japan, thus becoming the oldest production district and the beginning of the history of Japanese lacquerware.
Prosperity of the Echizen Urushi was relevant to Jodo Shinshu, also know as Shin Buddhism that was spread by Shinran, a Japanese Buddhist monk. The religion was widely believed in the area and he used three kinds of lacquer bowls to serve food to visitors who attended his lectures.
The lacquerware techniques were improved between Meiji (1868~1912) and Taisho (1912~1926) period. The forerunners in Echizen traveled all over Japan to search urushi’s habitation for superior urushi material and to study advanced techniques. They established the skills of creating many forms of the wooden base and decorating the lacquerware. Furthermore, the craftsmen often interact with other craftsmen in Kyoto and Wajima Sanchu, the famous lacquerware production areas, because of their readily accessible location.
Today, Echizen is continuously challenging to produce new lacquerware matching to the modern life style. There have also been many efforts to develop new material using latest technology. This has brought Echizen to the top shareholder (over 80%) today in the national market of business use lacquerware such as in hotels and restaurants.
- Scenes of people who worked at former urushi industry
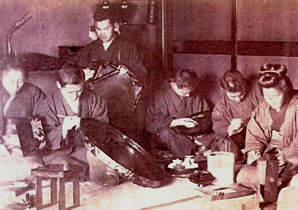
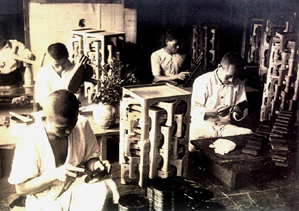
How to Create Echizen Urushi
- Creating the base forms
- Coating the surface with Urushi
- Decorations
There
are both wooden and plasticbase lacquerware. Creating round shape lacquerware
made of wood, involves the use of holding blades and carving shapes into
blocks of wood revolving on a wood lathe. If the base is made of a piece
of natural wood, it needs to be dried for at least 6 months. Box and tray
lacquerware made of natural wood or plywood must be dried for about 1 year
before cutting and carving into any shapes. On the contrary, plastic base
lacquerware is created with compressing wood or plastic powder using heat
process.
Two
layers of Urushi compose the lacquerware surface. The basecoat is applied
repeatedly the process through coating, drying, and filing. The base will
be covered by a topcoat, however, it is an essential part that reinforces
the base. Creating the topcoat requires increased skill, and the Urushi
must be applied with equal thickness. At the drying stage of the topcoat,
the temperature and humidity controls need to be set accurately. Both topcoat
and basecoat will take 3 months to complete. There are several ways to
apply the topcoat. The Shokunins use brush or spray depending on the shape
of the lacquerware.
Lacquerware
complete with beautiful decorations. One of the traditional painting techniques
is makie, and it is applied using gold and silver powders sifted over wet patterns
painted with urushi, and the parts are filed and polished to straighten the
patterns. Chinkin is another technique that adheres applications, such as powder
or gilt made from gold or silver, or colorant which is applied on carved patterns.
Besides these traditional works, nowadays a screen processing print is used
as an efficient decorating.Return to the top